Przemysł wrzuca czwarty bieg
Gdy firma produkcyjna zaczyna przygodę z cyfryzacją procesów, nie powinna rzucać się od razu na głęboką wodę. Wiele projektów łączenia informatyki (IT) z automatyką przemysłową (OT) upadało z tego tylko powodu, że klient chciał już na początku zbyt dużo osiągnąć.
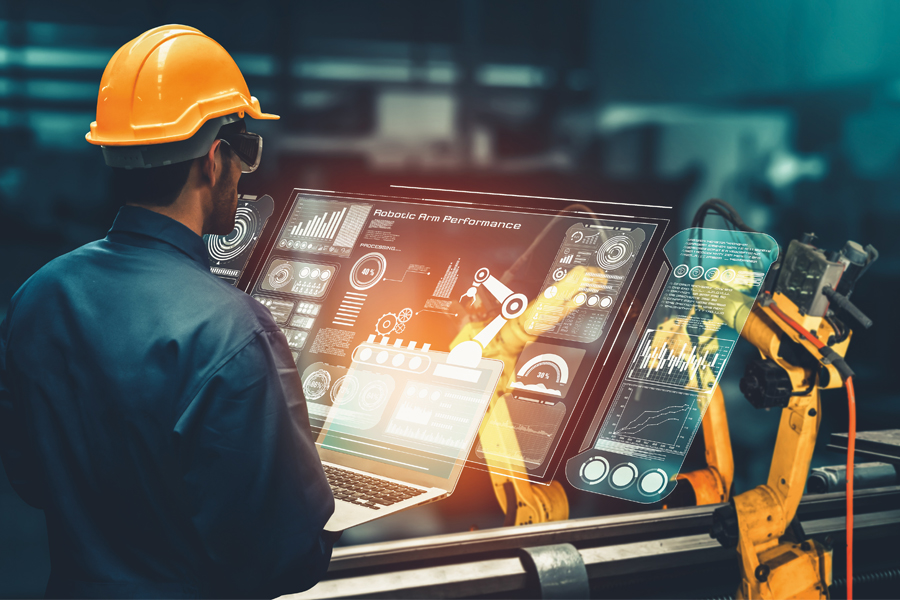
Firmy produkcyjne zwiększają poziom cyfryzacji i automatyzacji procesów.
Nie wszystko od razu
Rozpoczynając integrację OT z IT należy przede wszystkim zdefiniować swoje cele. Punktem wyjścia musi być określenie, co chce się osiągnąć z biznesowego punktu widzenia, a nie tylko podążanie za trendami technologicznymi. W tym drugim przypadku, gdy nie ma jasno sprecyzowanych celów, może się okazać, że efekt końcowy nie spełni oczekiwań zainteresowanych i trudno będzie uznać transformację za udaną.
A celów może być kilka. Jednym z nich będzie zdobycie przewagi konkurencyjnej – poprzez możliwość stworzenia produktu wyższej jakości czy też przyspieszenia tempa jego produkcji. Kolejnym celem może być uzyskanie oszczędności – poprzez znalezienie wszelkich synergii i zwiększenie efektywności produkcji. Celem może być również większa sprawność operacyjna – poprzez konsolidację rozproszonych, a często nawet powielonych kompetencji. A przy tym nie do pominięcia jest też możliwość poprawy bezpieczeństwa.
Gdy firma produkcyjna zaczyna przygodę z cyfryzacją procesów, nie powinna rzucać się od razu na głęboką wodę. Wiele projektów łączenia IT z OT upadało z tylko tego powodu, że klient chciał już na początku za dużo osiągnąć. Owszem, w przypadku maszyn trzeba jak najwięcej zaplanować od razu, bo potem trudno będzie coś zmienić. Inaczej jest jednak z informatyzacją i cyfryzacją produkcji, które powinny być wprowadzane stopniowo. Trzeba się też uzbroić w cierpliwość i założyć, że transformacja firmy produkcyjnej na pełną skalę będzie wymagać wielu miesięcy.
– Nie warto tworzyć od razu wielkiego projektu, zwłaszcza jeśli firma nie ma doświadczenia z cyfryzacją. Grozi to znacznym wydłużeniem czasu oczekiwania na pierwsze korzyści. Dużo łatwiej jest zacząć na małą skalę, nawet jednej maszyny. Projekt może dotyczyć automatyzacji zleceń produkcyjnych, archiwizacji danych czy wyeliminowania ręcznego raportowania, a efekty wdrożenia powinny być mierzone. Okaże się wtedy, na ile wdrożenie przyspieszyło komunikację, wyeliminowało błędy i przestoje, bądź usprawniło administrowanie – mówi Adrian Stelmach, Industrial IT Department Director w Amisterze.
Mierzenie efektów projektu przeprowadzonego na małą skalę da możliwość wprowadzania kolejnych poprawek. Obejmując wdrożeniem następne maszyny, będzie można poszerzać zakres pozyskiwanych danych, korelować te informacje z planem produkcyjnym, łączyć z funkcjami systemów ERP itp. Integrację powinno się zaczynać od pilota, aby zorientować się, jak to działa w praktyce. Nowe podejście do automatyzacji wymaga bowiem dodatkowych kompetencji i sprawdzenia, jak IT może pomagać OT, czego OT może od IT wymagać, jak oddzielne dotąd systemy „dogadują się” ze sobą.
Do stopniowego wdrażania elementów Przemysłu 4.0 – rozwiązań z zakresu sztucznej inteligencji, rzeczywistości wirtualnej, Internetu Rzeczy, big data – oraz mierzenia efektów transformacji nawiązał w wywiadzie dla CRN Polska Wojciech Grelecki, dyrektor IT w firmie SaMASZ, zajmującej się produkcją maszyn zielonkowych (nr 5/2022).
– Żeby cyfrowa fabryka przyszłości mogła sprawnie funkcjonować, potrzebne jest zbieranie i przetwarzanie danych z maszyn. Część z nich ma już czujniki, inne trzeba dopiero opomiarować. Będziemy to stopniowo robić ze względu na cyfryzację procesu produkcyjnego. Możliwości zastosowania optymalnych rozwiązań w tym zakresie będziemy badać w ramach tworzonego przez nas projektu Superfabryki Przemysłu 4.0 – wyjaśnia Wojciech Grelecki.
Integracja zwiększa ryzyko
Oczywiście łączenie obu światów wiąże się z podwyższonym ryzykiem cyberzagrożeń. Źle przeprowadzona integracja zwiększa powierzchnię ataku, ponieważ systemy automatyki przemysłowej nie były wcześniej częścią polityki bezpieczeństwa IT. W rezultacie typowe podatności środowiska OT to wciąż niska świadomość pracowników produkcji w zakresie cybersecurity, a poza tym nieautoryzowane punkty i metody dostępu, używanie domyślnych loginów i haseł czy współużytkowanie kont. Do tego dochodzą: nieuwzględniająca bezpieczeństwa architektura sieci, podatne protokoły oraz przestarzałe, niewspierane oprogramowanie i sprzęt.
Nie można zatem w nieprzemyślany sposób włączać do sieci informatycznej i zewnętrznego świata systemów automatyki przemysłowej oraz linii produkcyjnych, a także nieumiejętnie korzystać z nowych technologii i architektur, takich jak edge computing, IoT czy chmura. Jeśli więc Przemysł 4.0 wymaga pozyskiwania danych z OT, to konieczne staje się wypracowanie równowagi pomiędzy zapewnieniem dostępności i odpowiednim poziomem zabezpieczeń przed cyberzagrożeniami.
Zdaniem integratora
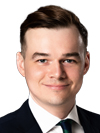
Technologie IT i OT mocno zbliżyły się do siebie. Widać to chociażby w programowaniu sterowników maszyn, które nie służy już wyłącznie odwzorowaniu schematów elektrycznych, wykorzystując wysokopoziomowe języki typu C. To ogromnie zwiększa zaszytą w sterownikach inteligencję i ich możliwości komunikowania się z systemami IT. Integracja obu światów prowadzi do tego, że w firmach produkcyjnych pomiędzy wcześniej odseparowanymi działami informatycznymi i automatyki przemysłowej tworzony jest dział pośredni, którego zadaniem jest połączenie różnych kompetencji. Ewentualnie firmy szukają zewnętrznego partnera, który podejmie się takiej misji. Chociaż nie mamy wielu danych o polskim rynku, to bazując na przykład na stopniu wykorzystania systemów ERP, można zakładać, że duże firmy produkcyjne mają już wdrożone elementy integracji IT i OT. Średnie i mniejsze podmioty są bez wątpienia na wcześniejszym etapie cyfryzacji produkcji. Do postępów na tej drodze może je skłaniać chęć optymalizacji kosztów i poprawy jakości, ale także wymogi standaryzacji narzucane przez większych partnerów biznesowych, dla których są poddostawcami.
Podobne artykuły
Industrial IoT: technologia w fazie rozwoju
Myśląca przyszłościowo i pragnąca zdobyć przewagę konkurencyjną firma z branży produkcyjnej stara się czerpać korzyści z łączenia technologii IT z automatyką przemysłową. Polega to najczęściej na wdrożeniach Przemysłowego Internetu Rzeczy (IIoT).
Przemysłowe IoT: skuteczna konwergencja IT i OT
Cyfryzacja zmienia sposób funkcjonowania przedsiębiorstw. Często jest określana jako czwarta rewolucja przemysłowa lub model Przemysłu 4.0, który polega głównie na automatyzacji procesów i korzystaniu z narzędzi bazujących na sztucznej inteligencji (AI) i uczeniu maszynowym (ML).
Optymalne zarządzanie w przemyśle 4.0
ATEN oferuje rozwiązania KVM over IP do zwiększania wydajności produkcji, centralnego sterowania oraz przeprowadzania bezpiecznych operacji. Znajdą one zastosowanie m.in. w zaawansowanych technologicznie środowiskach przemysłowych, takich jak fabryki układów scalonych, najnowocześniejsze linie montażowe czy działy kontroli jakości.